As part of its environmental policy, Germany has decided to phase out the use of coal by 2038. Many coal-fired power stations will cease all activity before this deadline. This is the case for Evonik, a major player in speciality chemicals, which has announced the closure of the coal-fired power station at its chemical park in Marl (Rhineland-Westphalia) in 2021.
This chemical park comprises several production units and around fifteen other chemical companies. While two new combined-cycle power stations are being built to ensure energy production, the closure of the coal-fired power station means that a solution must be found for the disposal of hazardous waste that was previously co-incinerated.
The ecological transition involves modernising and extending the existing incinerator, as well as building a new incineration line. To meet this challenge, SARPI has been building a brand new facility to treat the hazardous waste produced at the chemical park since 2020.
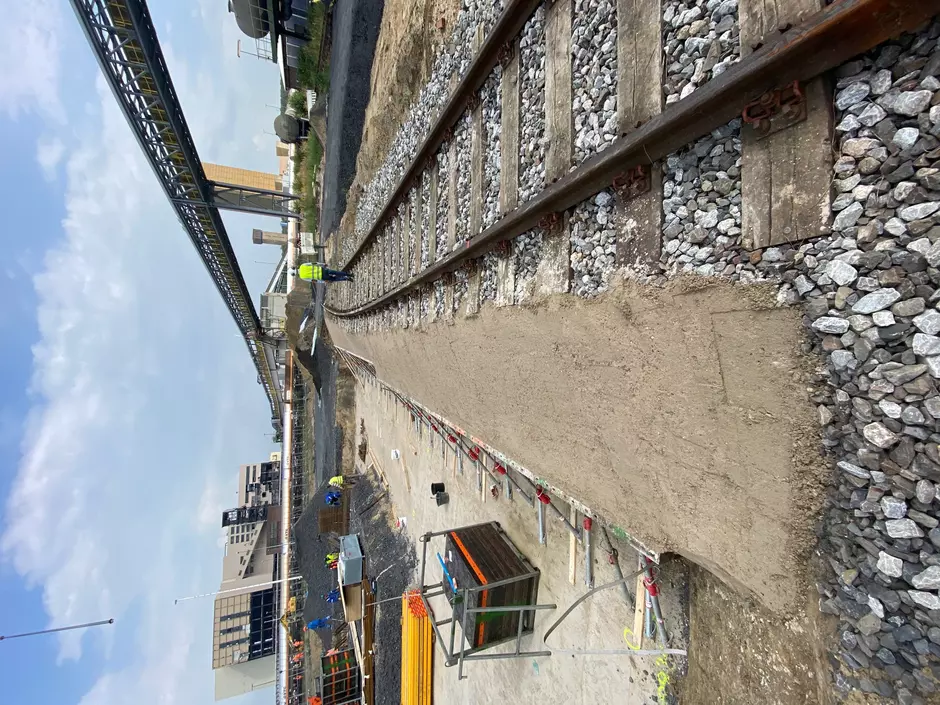
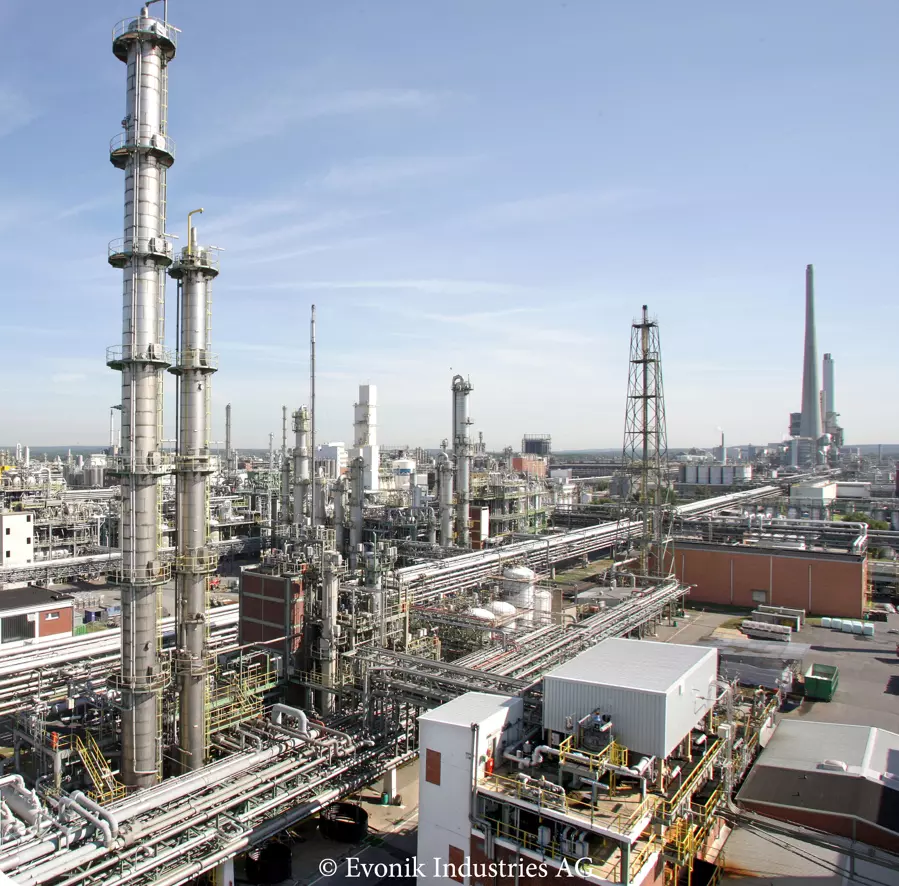
With the takeover of the existing incinerator and the construction of the largest incineration line in Europe, SARPI will have a total capacity for the thermal treatment and energy recovery of almost 250,000 tonnes of hazardous waste per year in Germany. The new facility will be able to treat all the hazardous waste from the Marl chemical park, as well as hazardous waste from the region's industrial companies. The energy produced will be 100% recycled into the chemical park's steam network, thereby reducing the impact of almost 100,000 tonnes of CO2 per year.
To support the ecological transformation of the Marl chemical park, SARPI is modernising the existing hazardous waste incinerator and building a new incineration line. It was essential to build upstream storage capacity for the liquid waste produced at the chemical park with a view to its future disposal. This is what our teams at Marl have achieved with the construction of a fleet of 16 storage tanks for different categories of liquid waste, with a total capacity of 2,800 tonnes. Construction began in August 2020 and is due to be completed by the end of 2021, with the facility coming on stream in time to handle the liquid waste previously co-incinerated in the coal-fired power station. A successful challenge for the project team and the first step towards our new plant in Germany!
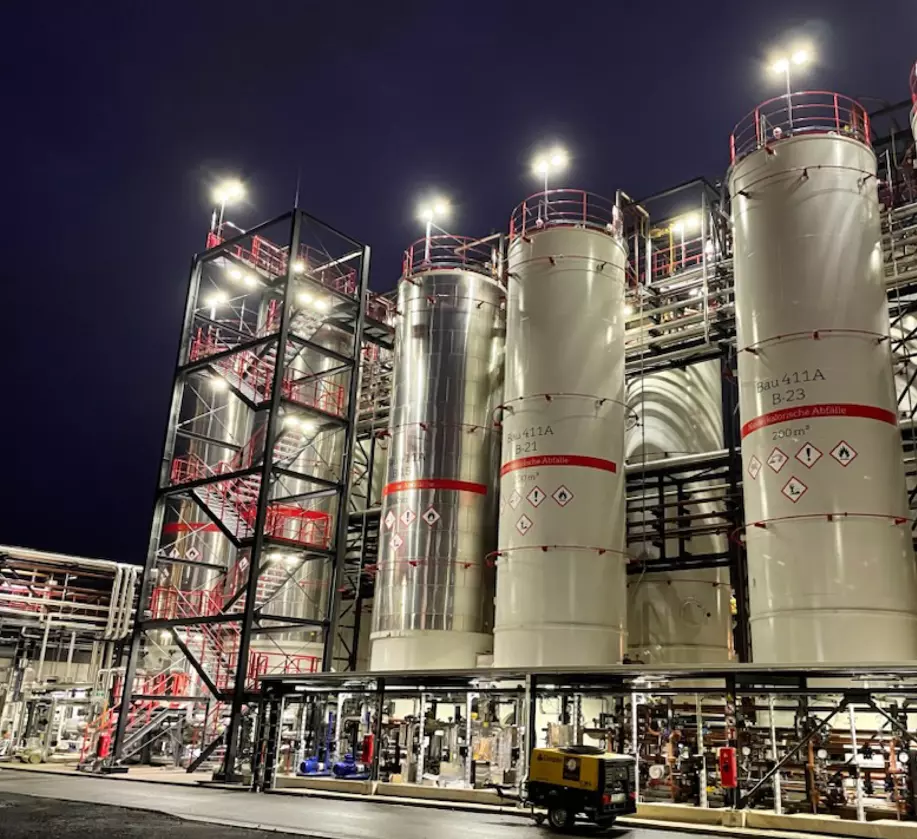
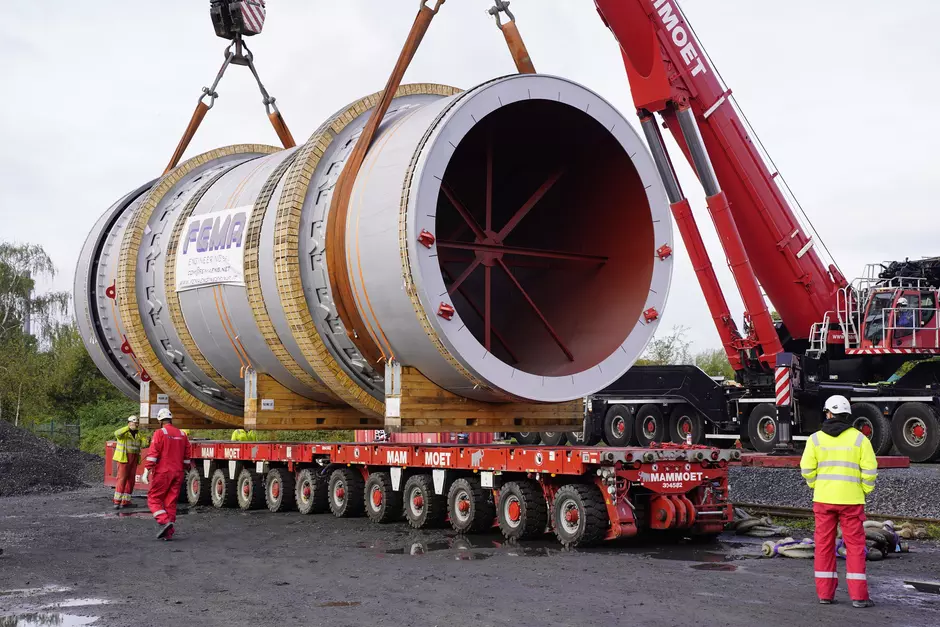
Construction work on the new incinerator is progressing apace, and the teams reached a new milestone at the end of October 2023 with the arrival and installation of the new rotary kiln.
Setting off from Bergamo (I) in September, the furnace travelled more than 6,000 kilometres over land and water in Italy, France, Spain and the Netherlands to Rotterdam, before arriving near the Marl chemical park by river barge.
The dimensions of this extraordinary operation
tons
meters long
meters in diameter
transport days in Europe
people mobilised
kilometers travelled in Marl
kilometers travelled in Europe
days transport in Marl
The arrival of the rotary kiln at Marl in pictures
An extraordinary project needs an extraordinary team!
The new laboratory!
Since the takeover of the RK2 incineration plant in the Marl chemical park in 2021, SARPI has been renting a laboratory while awaiting the construction of the brand new plant, also including a brand new laboratory!
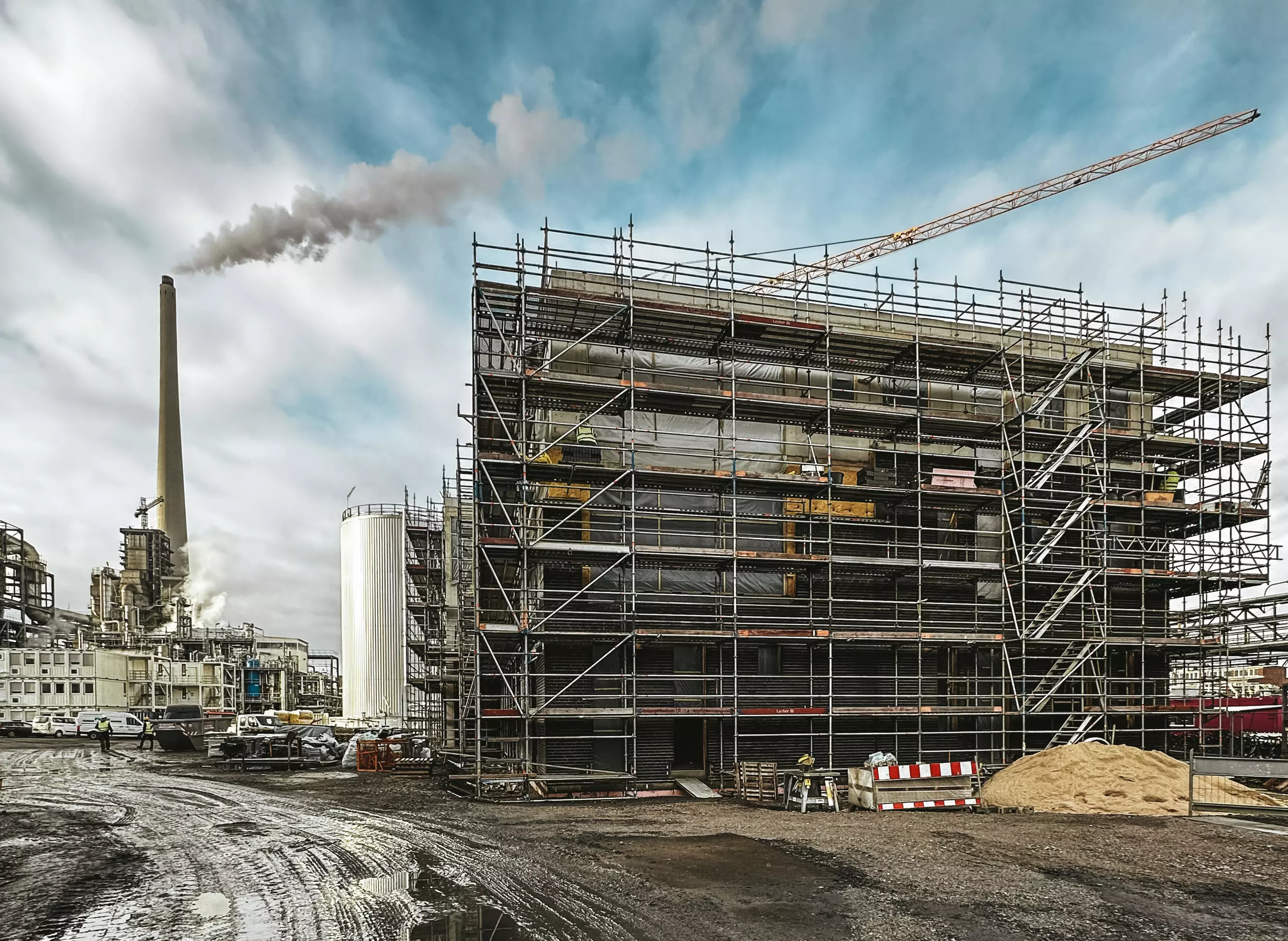
- The Marl laboratory is at the heart of the hazardous waste treatment process:
To guarantee the acceptability of waste on site, all waste is first analysed using a sample prior to receipt. No waste is accepted on site without systematic analysis on receipt, mixing tests and laboratory approval. - To ensure an optimal and safe incineration process, samples are analysed throughout the waste's journey.
- To declare waste clean at the plant, analyses are carried out on samples of materials.
The analyses carried out in the Marl plant laboratory include analyses such as:
- the calorimeter
- ion chromatography
- pH
- flash point
- determination of salts and heavy metals by XRF
With the creation of a new laboratory on the new incineration line, further analyses are planned, including ICP-OES (spectrometry) and determination of the organic load.
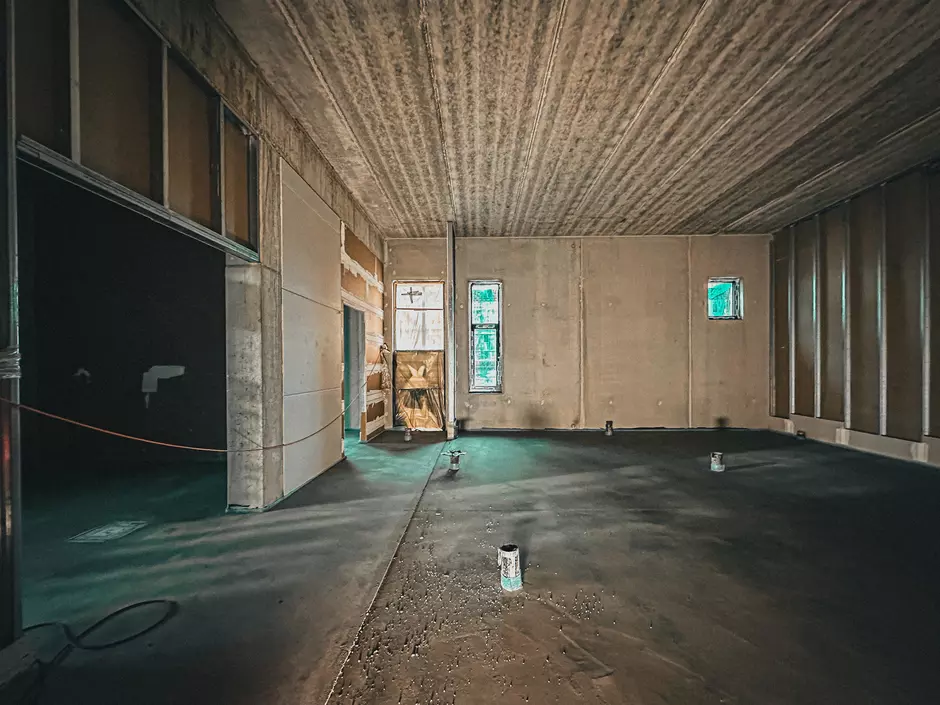
The Marl laboratory in figures:
- 30 to 40 samples received per day
- 7 to 10 analyses carried out on each sample (an average of 315 analyses per day)
- 4 laboratory assistants
With the creation of the new laboratory, analyses will be multiplied by 3 or 4 and a new laboratory technician will join the team already in place.
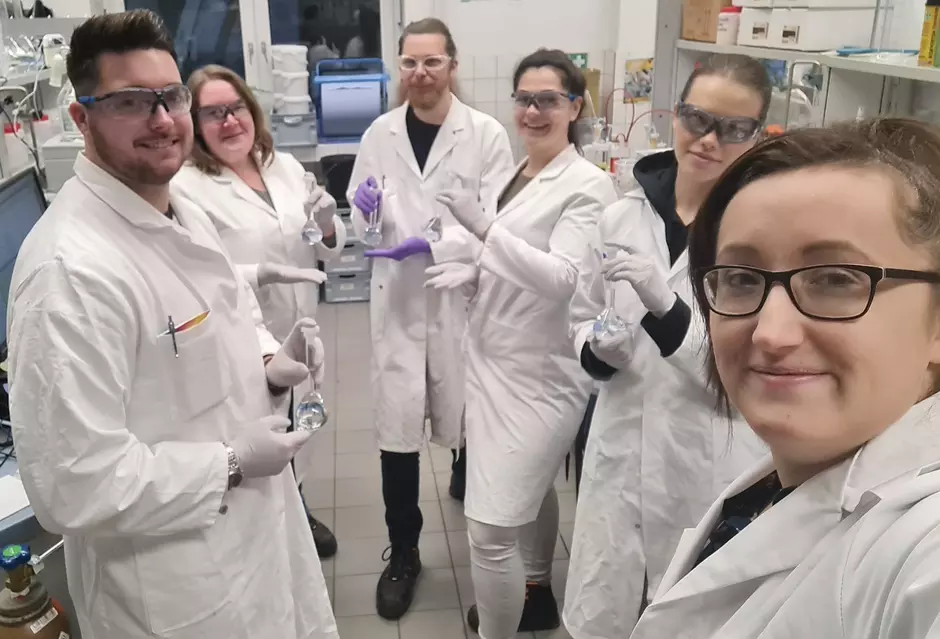
- In addition to their analysis work, the laboratory assistants are also involved in :
planning the input/output of treated waste - waste acceptance
- weighing the waste received
- notifications and national regulations on the transport of waste.
The new laboratory will offer more space and allow us to be at the heart of the system, promoting better information exchange.
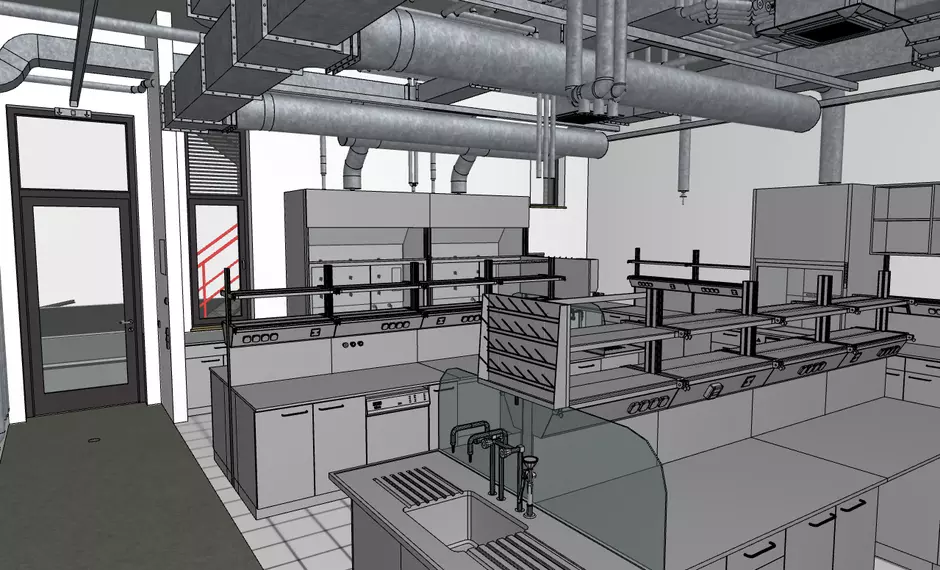
The new post-combustion chamber!
What is the role of the post-combustion chamber?
- The post-combustion chamber, located between the rotary kiln and the boiler, ensures that all the organic matter has been completely burnt.
At what point in the waste incineration process does the post-combustion chamber come into play?
- After being burnt in the furnace at 1,000°C, the waste enters the post-combustion chamber, where the gases are burnt to a final temperature of over 900°C.
- The resulting bottom ash (combustion residue) is recovered under the post-combustion chamber, while the gases rise in the chamber and continue their journey through the boiler and on to the flue gas treatment system.
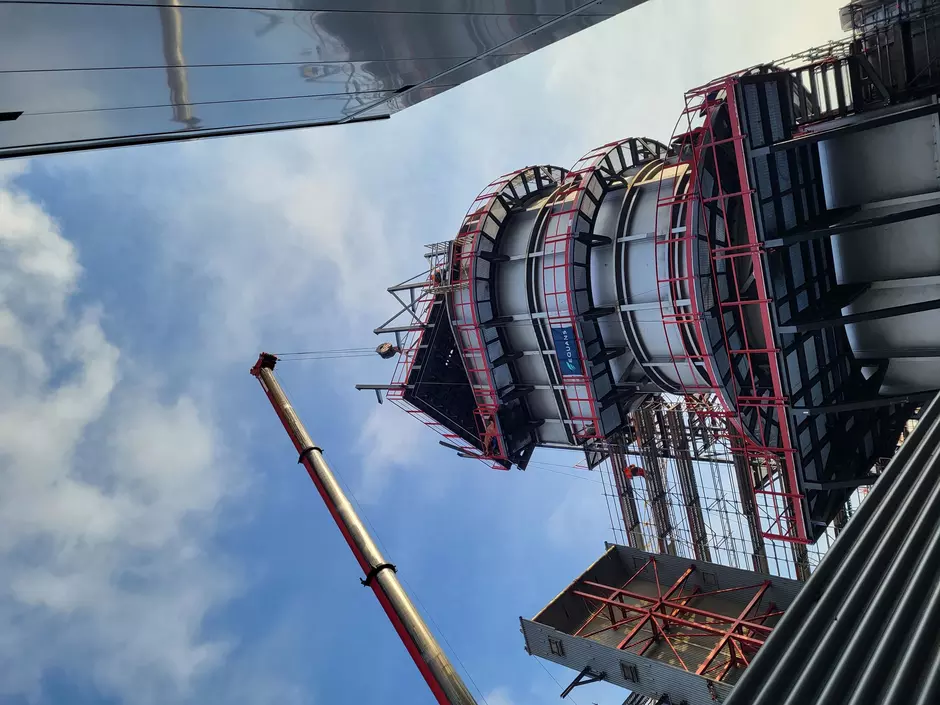
The new post-combustion chamber in figures:
- 24 metres high
- 8.4 metres in diameter
- 2 burners
- 8 low-calorific lances
- temperatures ranging from 900°C to 1100°C
- 1 emergency chimney
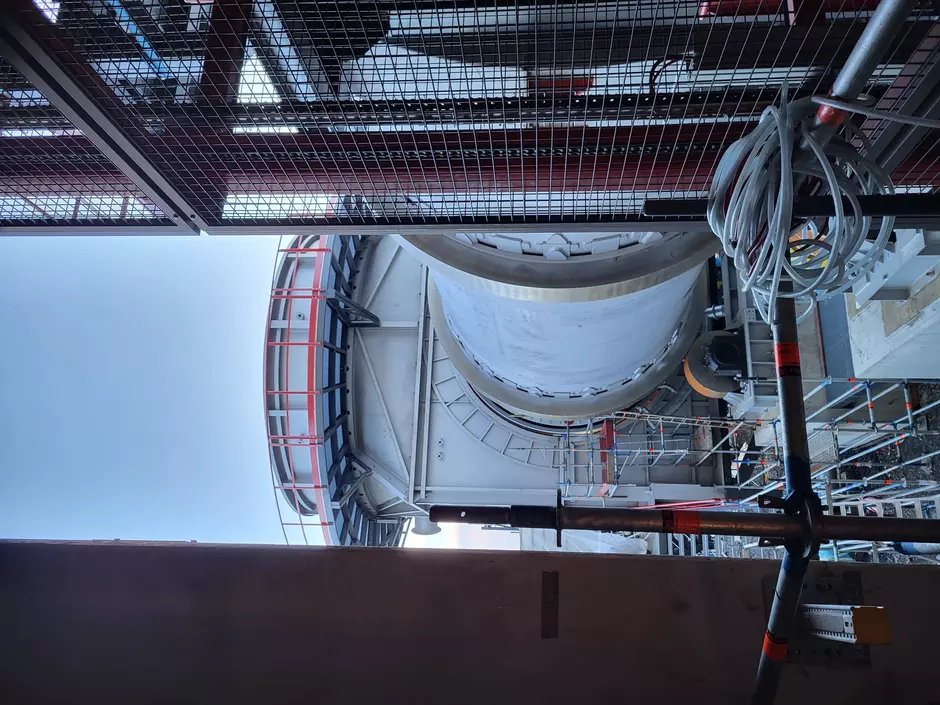
The new boiler!
What is the role of the boiler?
The heat recovery boiler cools the gases from the post-combustion chamber and produces steam.
What does this new boiler consist of?
- 3 empty paths (radiant part)
- 1 tail-end (convective part) itself made up of :
- 2 evaporators
- 3 superheaters (High Temperature, Medium Temperature and Low Temperature),
- economisers
- Separator tank on the roof of the boiler
- Food tank on a platform next to the boiler
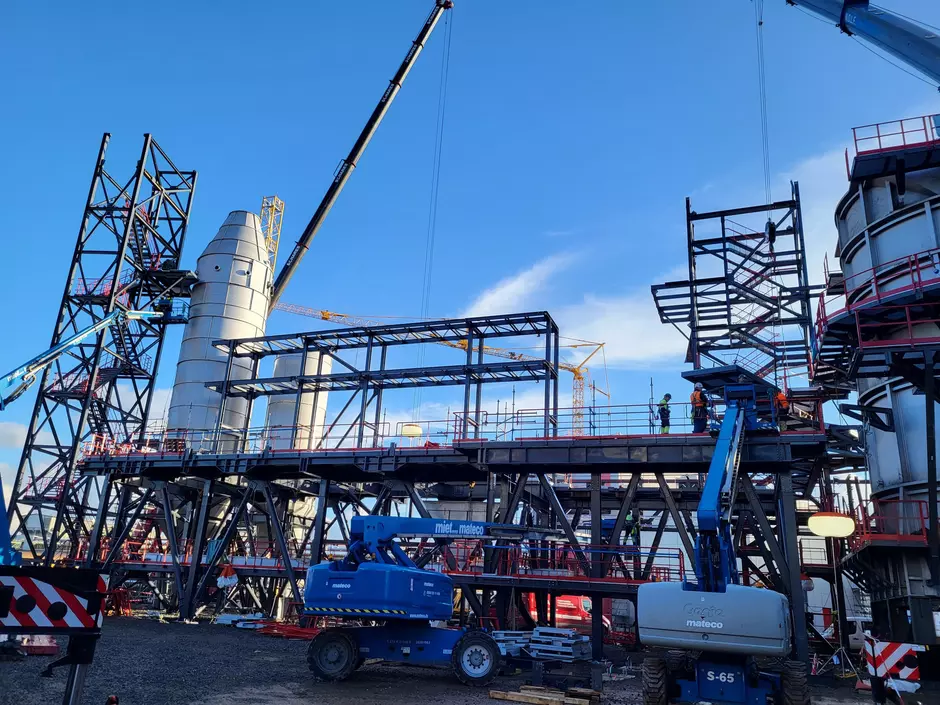
In practical terms, how does it work?
Throughout the process, demineralised hot water is introduced as required. This maintains the required level in the boiler tank to compensate for steam production and losses due to blowdown.
The superheated steam produced (43.5 bar a, 380°C) is sent to a back-pressure turbine, then to the Marl chemical park steam network (20 bar a). Once cooled by passing through the boiler, the flue gases enter the flue gas treatment process. The ash from the gases is then removed from the vertical section by two conveyor belts. Ash from the horizontal section is removed by a trough chain conveyor.
The new boiler in figures:
- 29 metres high
- 31 metres long
- 7.5 metres wide for the vertical section
- 4 metres wide for the horizontal section
- Gas inlet temperature: 900°C - 1100°C
- Gas outlet temperature: 245°C
- Superheated steam production: 49.8 t/h